All CPA Business Environment and Concepts (BEC) Resources
Example Questions
Example Question #1 : Technology Process Management
Which of the following is not a characteristic of Total Quality Management?
Continuous Improvement
Customer Focus
Quality Circles
Waste Reduction
Waste Reduction
TQM focuses on customer needs, continuous improvements, and quality circles. Waste reduction is a quality of lean manufacturing, not TQM.
Example Question #2 : Technology Process Management
Which of the following management philosophies does not focus on quality?
Gap Analysis
Total Quality Management
Lean
Absolute conformance
Lean
The main objective in lean manufacturing is waste reduction. Although customer requirements and demand pull serve as the basis for the approach, quality is not the most prominent concept.
Example Question #201 : Cpa Business Environment And Concepts (Bec)
Which of the following uses analysis of production processes to ensure that resource uses stay within target costs?
Value Chain Analysis
Just-in-time
Activity based costing
Kaizen
Kaizen
Kaizen, or continuous improvement, occurs at the manufacturing stage where the ongoing search for cost reductions takes the form of analysis of production processes to ensure that resource uses stay within target costs.
Example Question #4 : Technology Process Management
Which of the following is not a requirement of just in time systems?
Strong job specialization
Employee empowerment
Supplies received as needed throughout the day
Reduced setup time
Strong job specialization
Just in time means that employees with multiple skills are used more efficiently and will not specialize in merely one job or task.
Example Question #5 : Technology Process Management
Which of the following is not a typical characteristic of a just in time production environment?
Lot sizes equal to one
Insignificant setup times and costs
Push through system
Balanced and level workloads
Push through system
Just in time has the goal to minimize the level of inventory carried. It has a pull approach rather than a push approach.
Example Question #6 : Technology Process Management
There are 7 factors critical to total quality management. Which is not one of them?
Objective measures
Timely recognition
Executive compensation
Customer Focus
Executive compensation
Total quality management focuses on a customer-focused experience and compensation of the executives has no bearing on a customer.
Example Question #1 : It Governance
A research-based firm in the medical field could use each of the following Internet-based tools for collaboration except:
Groupware systems
Videoconferencing
Electronic data interchange
An email application
Electronic data interchange
EDI is a computer to computer exchange of business transaction documents. It is not used for collaboration between humans.
Example Question #1 : Technology Process Management
Engaging in traditional electronic data interchange (EDI) provides which of the following benefits?
Reduced likelihood of stockout costs
Added flexibility to entice new partners
Guaranteed payments from customers
Enhanced audit trails
Reduced likelihood of stockout costs
EDI is the exchange of business transaction documents from one computer to another. This is much more efficient than paper exchanges and reduces the likelihood of stockout costs.
Example Question #2 : Technology Process Management
All of the following statements regarding project risk are correct except:
Risk control includes anticipating everything that could go wrong throughout the project plans
There is always a tradeoff between risk and reward
Planning for risk management includes risk assessment
Risk is inherent in every aspect of the project management process
Risk control includes anticipating everything that could go wrong throughout the project plans
Anticipating everything that could go wrong throughout the project plans is a part of risk assessment, not risk control.
Example Question #3 : Technology Process Management
A manufacturer that wants to improve its staging process compares its procedures against the check-in process for a major airline. Which of the following tools is the manufacturer using?
Benchmarking
Total quality management
Economic value added
Statistical process control
Benchmarking
Benchmarking is a process where a company compares itself to peers to measure performance and to understand where improvements can be made in its processes.
Certified Tutor
Certified Tutor
All CPA Business Environment and Concepts (BEC) Resources
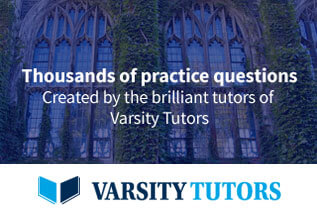